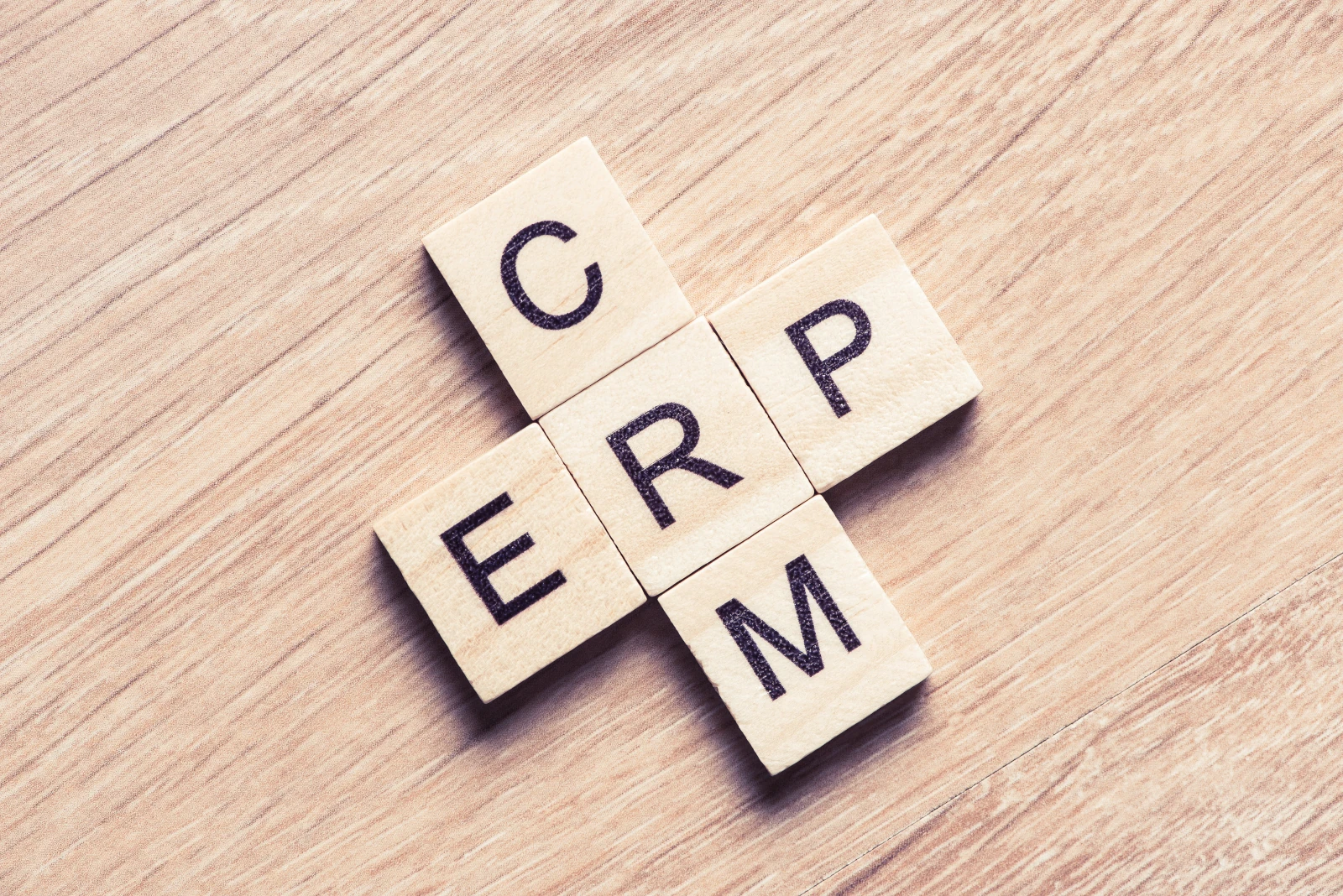
Modern companies increasingly use tools to improve customer relationships and business process management regardless of industry. One key solution is a CRM system, which helps build and maintain long-term customer relationships. What exactly is a CRM? What are its types and capabilities? Most importantly, how does it differ from ERP?
What is a CRM? What does the acronym stand for?
CRM stands for customer relationship management. A CRM system is an IT tool that assists companies in serving customers, collecting sales data, and automating marketing processes.
With a CRM system, a company can monitor the history of interactions with customers, analyze their behavior, and personalize offers. Thus, the key function of CRM systems is to build and maintain lasting relationships with customers through effective data management and sales processes.
CRM system - what does it consist of?
A CRM system centralizes and organizes customer information in one place. It is a database containing the history of contacts, transactions, complaints, and customer preferences and needs.
This allows sales, customer service, and marketing staff to:
- respond faster to customer inquiries,
- personalize offers,
- automate sales and marketing processes,
- analyze data, and predict customer behavior.
The main goal of the CRM system is to increase the efficiency of sales activities and improve the quality of customer service.
Application of CRM systems
CRM systems are used in various industries and sectors of the economy. Companies use CRM for, among other things:
- Customer database management - CRM allows for the storage of contact information, purchase history, and customer preferences.
- Automating sales processes - The system helps plan sales activities, generate offers, manage the sales funnel, and report results.
- Customer service - CRM enables efficient customer requests, complaints, and technical support management.
- Marketing and promotional campaigns - CRM systems allow you to segment customers, target advertising campaigns, and analyze the effectiveness of marketing activities.
- Data analysis and reporting - Advanced CRM systems provide tools for analyzing sales, forecasting market trends, and monitoring team performance.
CRM system – types
There are many different CRM systems available on the market, which can be divided into three main categories:
- Operational CRM focuses on automating sales, marketing, and customer service processes. It helps sales teams in their daily work and improves the quality of service.
- Analytical CRM processes and analyzes customer data. It enables customer segmentation, analysis of sales performance, and forecasting of market trends.
- Campaign CRM is mainly dedicated to marketing departments and supports running advertising campaigns and automating promotional activities.
Some CRM systems combine features of different types, offering comprehensive solutions tailored to a company’s specifics.
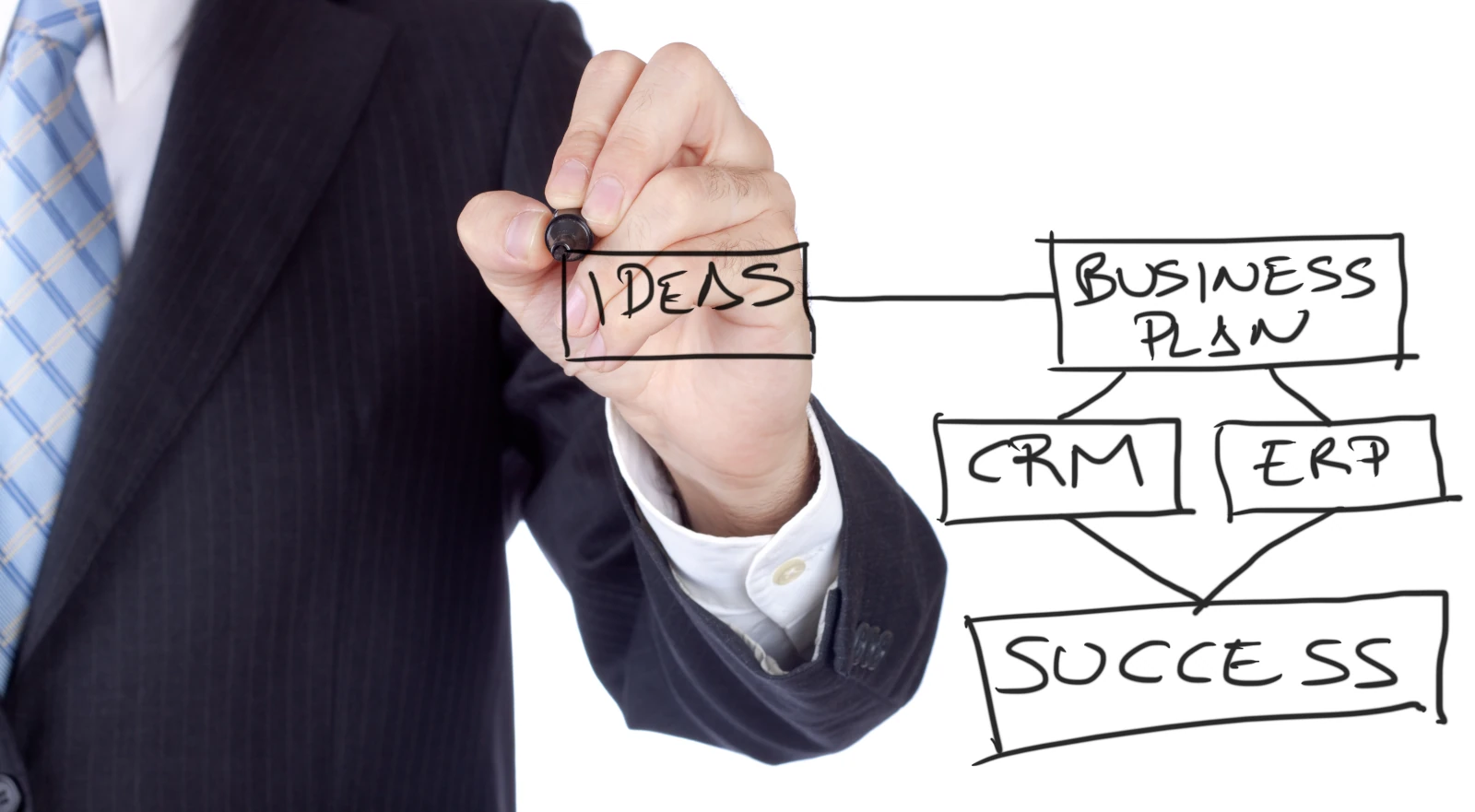
Capabilities of CRM systems
Modern CRM systems offer various functionalities that help manage customer relationships and improve sales processes. Here are some of them:
- Contact management - a customer database with filtering, sorting, and segmentation capabilities.
- Sales process automation - the CRM system can generate offers, remind follow-ups, and record customer interactions.
- Handling customer requests - manage complaints, inquiries, and service requests.
- Tracking customer activity - monitor e-mails opened, website visits, and purchase history.
- Reporting and analysis - generating sales reports, analyzing the results of marketing campaigns, and forecasting trends.
With these features, CRM allows companies to operate more efficiently, minimize the risk of losing customers, and increase loyalty.
CRM vs ERP - what is the difference?
Many entrepreneurs wonder how a CRM system differs from an ERP system. Both solutions help manage the company but have different goals and functionalities.
- CRM (Customer Relationship Management) - focuses on customer relationships. Its main goal is to optimize sales, marketing, and customer service processes.
- ERP (Enterprise Resource Planning) - is a system for managing enterprise resources. It covers finance, logistics, production, human resources, and many other company areas.
Main differences between CRM and ERP:
- CRM focuses on the customer, while ERP focuses on resources and internal processes.
- CRM supports sales and marketing, while ERP helps plan and manage company resources.
- ERP covers many business operations, while CRM specializes in customer relationship management.
In practice, many companies integrate CRM and ERP to automate business processes further.
A CRM system is indispensable for companies that want to manage customer relationships effectively. It allows companies to automate sales processes, analyze data, and personalize offers.
Different types of CRM systems are available on the market and can support operational customer management and analytical data processing.
Although CRM and ERP are often confused, they perform different functions – CRM focuses on the customer, while ERP focuses on company resources. Integrating the two systems usually allows for even better business management.
With modern CRM systems, companies can increase sales, improve customer service, and build long-term relationships, which translates into market success.