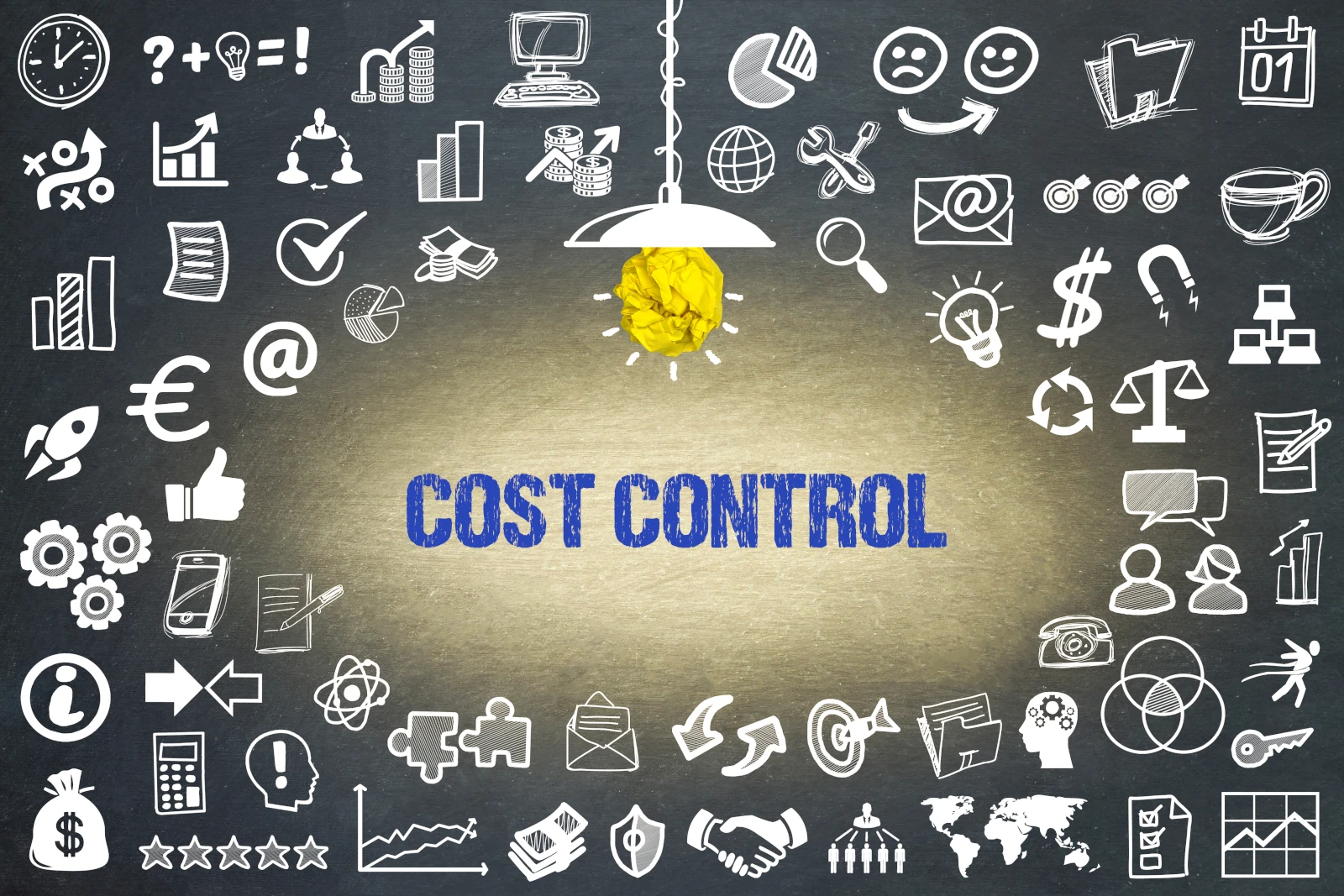
Production costs are a key component of business management. Proper analysis and optimization allow companies to achieve higher profitability and better compete in the market. We explain production cost, how to calculate it, and what formulas can be used in production costing.
Cost of production - what is it?
Cost of production is the total financial outlay incurred by a company to produce goods or services. It includes both direct and indirect expenses related to the production process. Depending on the specifics of the business, production costs can vary significantly, but they always consist of key elements, such as:
- Direct costs - refer to raw materials, materials, and wages of workers directly employed in production.
- Indirect costs include management, machinery maintenance, energy, logistics, and other expenses supporting production.
- Variable costs - their amount depends on the scale of production, e.g., raw material consumption and energy cost.
- Fixed costs are independent of the volume of production, such as rent for the production hall and depreciation of machinery.
Production costs - how to calculate?
Calculating production costs is key to the enterprise’s effective financial management. There are several methods to determine the expenses associated with producing products or services accurately. The basic approach to the calculation includes:
- Identifying direct and indirect costs - the first step is to identify all costs associated with production.
- Dividing costs into fixed and variable allows a more precise calculation of unit costs.
- Calculating unit cost: The unit cost of production is calculated by dividing total production costs by the number of units produced.
- Consideration of indirect costs—The method of allocating indirect costs based on established allocation ratios is often used.
Calculation of production costs
Production costing is necessary to determine the profitability of operations. The most common methods of production costing are:
- Apportionment calculation - used in mass production- divides total costs into product units.
- Additive calculation - used in unit and small batch production, where costs are added to a specific order.
- Standard costing - involves comparing actual production costs with normative costs to analyze deviations.
Correct calculation of production costs allows companies to accurately determine the selling price of products, which is crucial for their competitiveness.
Cost of production formula
To accurately calculate the cost of production, the following formula can be used:
KP = KB + KZ + KS
Where:
- KP - production cost,
- KB - direct costs,
- KZ - variable costs,
- KS - fixed costs.
In addition, the unit cost can be calculated according to the formula.
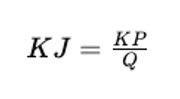
Where:
- KJ - unit cost,
- KP - total cost of production,
- Q - number of units produced.
Production costing formulas and methods allow companies to budget more effectively and optimize expenses. Companies that systematically monitor and analyze production costs can better manage their resources and maximize business profitability.