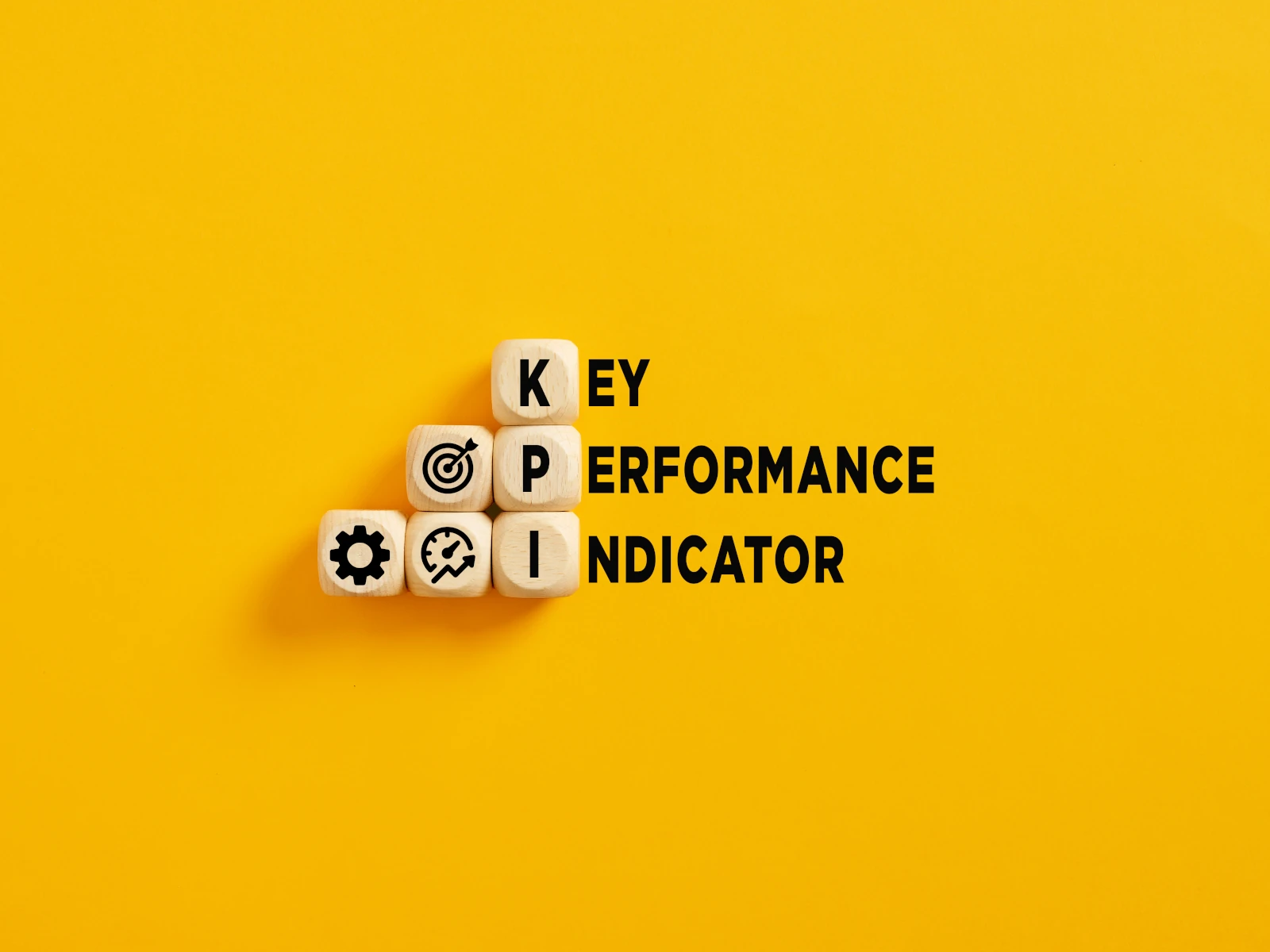
Measuring the efficiency of production processes is vital to the success of any company in the manufacturing industry. To achieve optimal results, it is necessary to monitor strategic performance indicators, or so-called KPIs (Key Performance Indicators). What KPIs are most important in manufacturing, and how do you monitor them for success? You will read all about it below.
What is a KPI?
KPIs, or key performance indicators, are used to measure progress and success in achieving a company’s strategic goals. In the context of manufacturing, KPIs measure the efficiency of production processes, labor efficiency, machine utilization, and the quality of manufactured products. These indicators are an indispensable part of operations management, allowing businesses to analyze production performance continuously and make decisions to improve efficiency.
KPIs help production managers keep track of various aspects of operations and respond to any irregularities. They help identify areas that need improvement, as well as monitor changes in performance over time.
Manufacturing KPIs - how to determine them?
Determining production KPIs is the first step to building a productive management system. The choice of KPIs depends on the specifics of the business, business goals, and company strategy. However, regardless of the industry, some fundamental indicators that can provide valuable information about the production process are worth considering.
- Overall Equipment Effectiveness (OEE) - a machine efficiency indicator that measures how healthy machines are used in production, considering availability, productivity, and quality.
- Production efficiency - an indicator that measures how many products are produced per unit of time. This indicator helps determine how quickly and efficiently production lines operate.
- The number of defective products is an important indicator of production efficiency, which informs about the quality of the products produced. The lower the indicator, the better the quality of production processes.
- Cost per production unit - a KPI that shows how much it costs to produce one product unit. Lowering this indicator is often crucial to optimizing operating costs.
These indicators must be regularly monitored, analyzed, and compared with the set targets.
Examples of KPIs – manufacturing
Choosing the right KPIs is challenging for many manufacturing companies, so it is helpful to know examples of indicators that work well for different companies. Here are some key manufacturing KPIs that you may find useful:
- OEE (Overall Equipment Effectiveness) - measures the use of equipment in the production process. It is calculated by multiplying machine availability, productivity, and product quality.
- Downtime - measures how long machines or production lines are out of service, which can be due to breakdowns, maintenance, or other problems. Reducing downtime is vital to increasing efficiency.
- Defect rate - measures the number of defective products relative to the total number of units produced. A high defect rate means that the production process needs to be optimized.
- Unit production cost - This indicator helps us understand how much it costs to produce one unit of product. Reducing this indicator is crucial in increasing profitability.
- Lead Time - an indicator that measures the time from order placement to delivery of the finished product. Reducing lead time is extremely important for customer satisfaction.
These examples are only a tiny part of the indicators used in manufacturing companies. Tailoring them to the specifics of your business and manufacturing processes is essential.
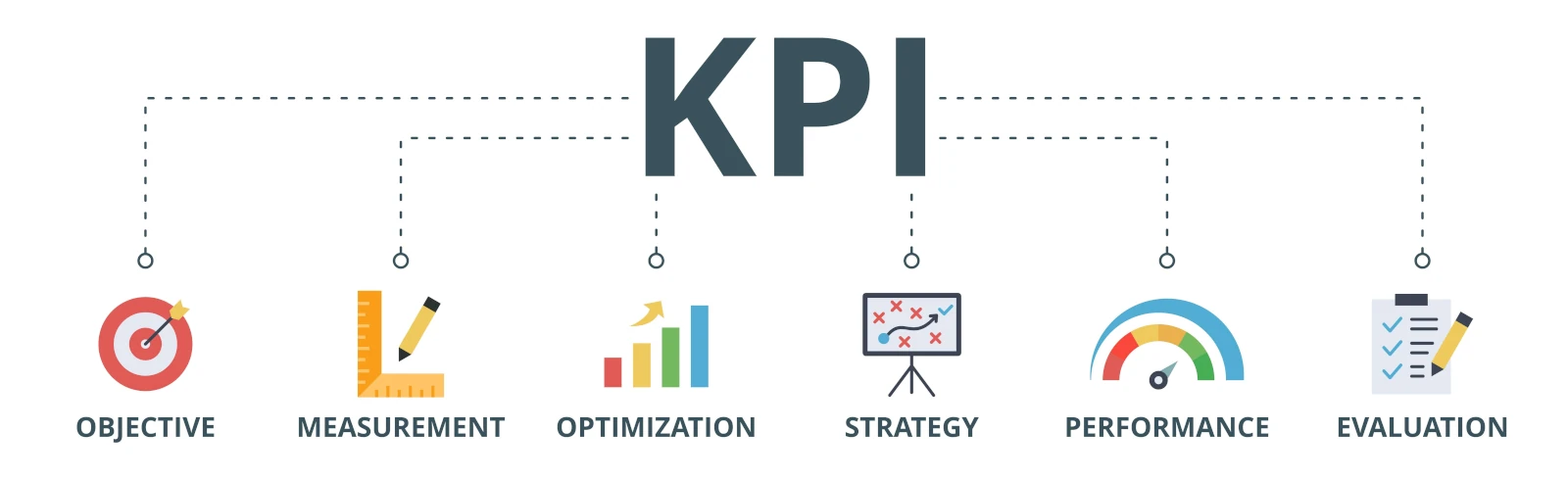
Why is it essential to set manufacturing KPIs?
Implementing production KPIs is the basis for optimizing production processes. Regular monitoring of KPIs allows you to understand which elements need improvement and what actions need to be taken to increase efficiency. Manufacturing KPIs have several key advantages:
- Process optimization allows you to analyze the performance of machines, people, and the entire production line in real-time. This will enable managers to identify problems and make appropriate changes quickly.
- Cost control - KPIs allow the company to identify areas where it can reduce production costs, thereby increasing profit margins.
- Improving quality - Indicators such as the number of defective products help identify quality problems, which in turn helps improve production standards.
- Increasing productivity - KPIs allow production managers to assess how well the company's resources are used, leading to increased productivity.
- Anticipate future needs - KPIs help plan resources and forecast future production requirements.
Practical determination of KPIs allows manufacturing companies to control production better, improve efficiency, and optimize costs.
How do we monitor production KPIs?
Monitoring production KPIs is a crucial element in managing a manufacturing company. The right tools and technologies can significantly facilitate this process. Here are some ways to effectively monitor KPIs:
- ERP systems - Enterprise resource management systems, such as ERP, allow you to track production efficiency, machine downtime, production costs, and other key performance indicators in real-time. This gives managers complete control over production and will enable them to react quickly to changing conditions.
- APS software - APS (Advanced Planning and Scheduling) systems enable advanced production planning and scheduling, which in turn allows efficient resource use and monitoring of KPIs.
- Dashboards - Modern technologies offer interactive dashboards that allow real-time monitoring of KPIs. These allow you to quickly identify problems and take appropriate action.
Monitoring production performance indicators with the help of advanced tools and IT systems allows businesses to manage resources and quickly respond to emerging challenges optimally. This is a critical element in building a competitive advantage in the market.